Power Plants
Empowering Power Plant Performance
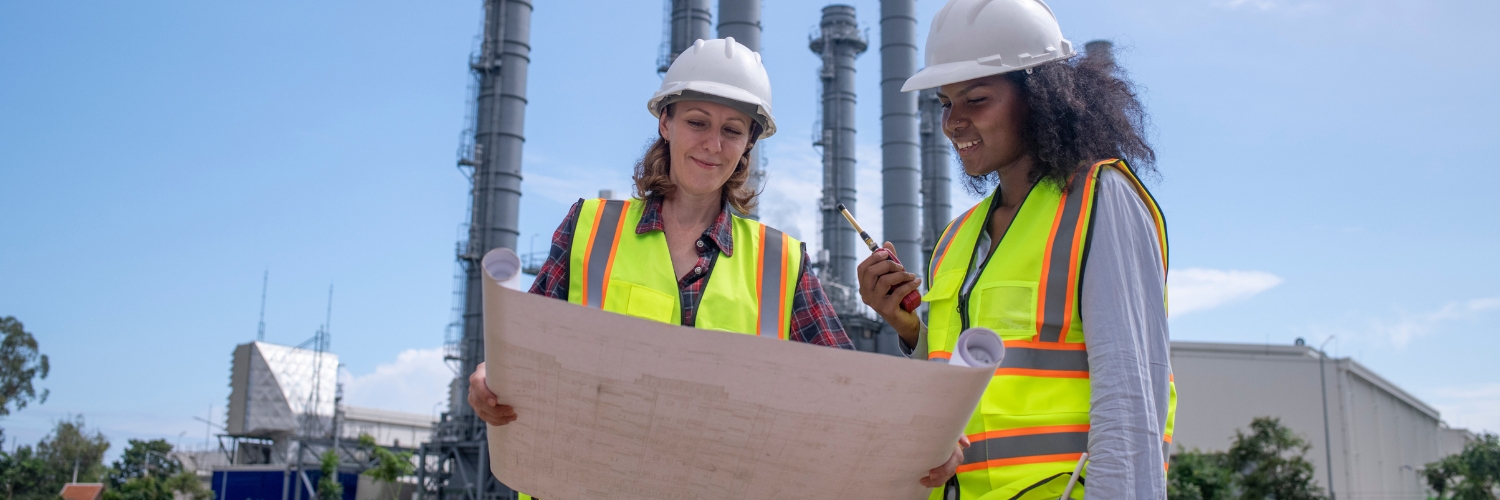
Strategic Initiatives in Action
Unlocking Reliability, Efficiency, and Cost Savings Through Condition Monitoring, RCM Strategies, and AP-913 Compliance
- Reduced maintenance overruns from 25% to 5%
- Improved ability to manage asset heath and align reliability processes with the AP-913 requirements
- Increased boiler efficiency through more efficient and effective ash and fly ash removal.
- Efficiency improvement for the Warehouse through several initiatives including BOM and MIN/MAX reviews and introduction of parts criticality.
- Improved maintenance scheduling by focusing on the work control management cycle from work request to execution and defining roles and responsibilities.
At one power plant, a shift toward proactive maintenance and strategic oversight transformed their operations. By implementing online condition monitoring, the team gained the visibility needed to manage asset health more effectively, ensuring reliability processes aligned with AP-913 requirements. With a clear understanding of equipment criticality, they were able to prioritize maintenance tasks, directing efforts where they would have the greatest impact.
Reducing overruns, boosting efficiency, and raising reliability.
This new approach paid off quickly. Maintenance overruns on the coal handling system dropped from 25% down to just 5%, thanks to revamped strategies guided by Reliability-Centered Maintenance principles. Boiler efficiency also improved dramatically. Although the equipment had the capacity to meet demand, its potential had been held back by ineffective maintenance and poor execution. More disciplined strategies and better execution of ash and fly ash removal processes removed these barriers, resulting in more consistent performance.
Ready to Achieve Results Beyond Expectations?
In the warehouse, reviewing Bills of Materials and implementing strategic MIN/MAX levels based on parts criticality streamlined inventory management and reduced costly downtime. Additionally, a refined work control management cycle—one that clearly defined roles and responsibilities and included the production team in planning—improved maintenance scheduling from start to finish.
In short, by embracing proactive maintenance approaches, aligning with industry standards, and integrating the entire team in the process, the power plant transformed once-faltering operations into a model of reliability, efficiency, and cost-effectiveness.