Tratamiento de aguas residuales
Garantizar un flujo constante de fiabilidad
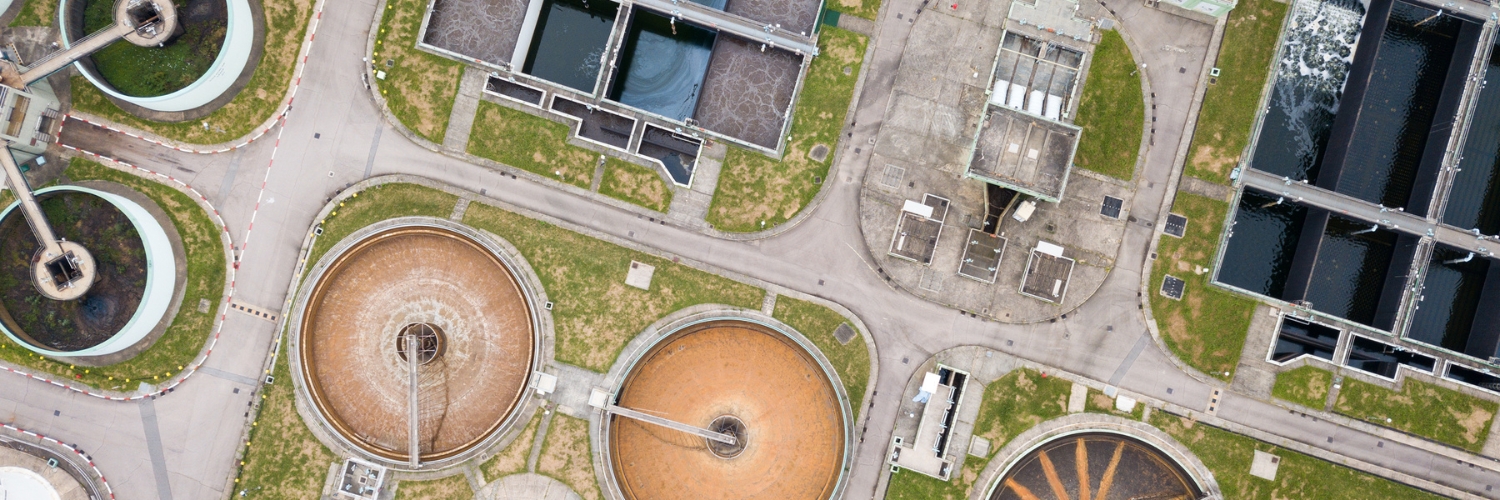
Garantizar un flujo continuo
Cómo el mantenimiento proactivo y la programación estratégica lograron una disponibilidad del 97% en medio de una demanda creciente
- Aumento de la disponibilidad de la línea al 97% mediante RCM y un análisis de riesgos y criticidad.
- Se abordó el rápido crecimiento de la población optimizando los programas de mantenimiento con FMEA, PMO, cuidado de activos por parte de los operadores y calendarios de paradas sincronizados.
A medida que las comunidades crecen, se intensifican las exigencias a las plantas de tratamiento de aguas residuales. Una de ellas se enfrentaba al doble reto de aumentar su capacidad de tratamiento y reducir al mínimo los tiempos de inactividad. Para lograrlo, el equipo adoptó el Mantenimiento Centrado en la Fiabilidad (RCM) y realizó un exhaustivo análisis de riesgos y criticidad. Al identificar y abordar los aspectos más vulnerables de sus sistemas, aumentaron la disponibilidad de la línea hasta un impresionante 97%. Esta alta fiabilidad no sólo permitió aumentar el rendimiento, sino que también garantizó que las infraestructuras esenciales satisficieran las necesidades cambiantes de la comunidad.
Alcanzamos una disponibilidad del 97% sincronizando el mantenimiento con el ritmo operativo de la planta, al ritmo de las necesidades de una comunidad en crecimiento.
Para prosperar realmente bajo las crecientes presiones demográficas, la planta necesitaba algo más que equipos robustos: necesitaba una estrategia de mantenimiento flexible y proactiva. Mediante el análisis de los modos de fallo y sus efectos (AMFE) y las iniciativas de la PMO, rediseñaron los programas de mantenimiento teniendo en cuenta las opiniones de los operarios. La introducción del cuidado de los activos por parte de los operarios permitió a los trabajadores de primera línea detectar los problemas a tiempo y mantener los sistemas en perfecto funcionamiento.
¿Listo para lograr resultados que superen sus expectativas?
Estas mejoras también se extendieron a la forma en que la planta gestionaba los cierres y las interrupciones. Al alinear las actividades y frecuencias de las paradas con el programa de producción, el equipo sincronizó las ventanas de mantenimiento con el "latido" de las operaciones de la planta. El resultado fue una interacción perfecta entre el mantenimiento y la producción, lo que garantizó que el tiempo de inactividad se redujera al mínimo y el rendimiento se maximizara, incluso cuando las necesidades de la comunidad circundante seguían creciendo.