Ferrocarril
Mantener la vía: Mantenimiento proactivo y diseño inteligente para unas operaciones ferroviarias más seguras y fiables
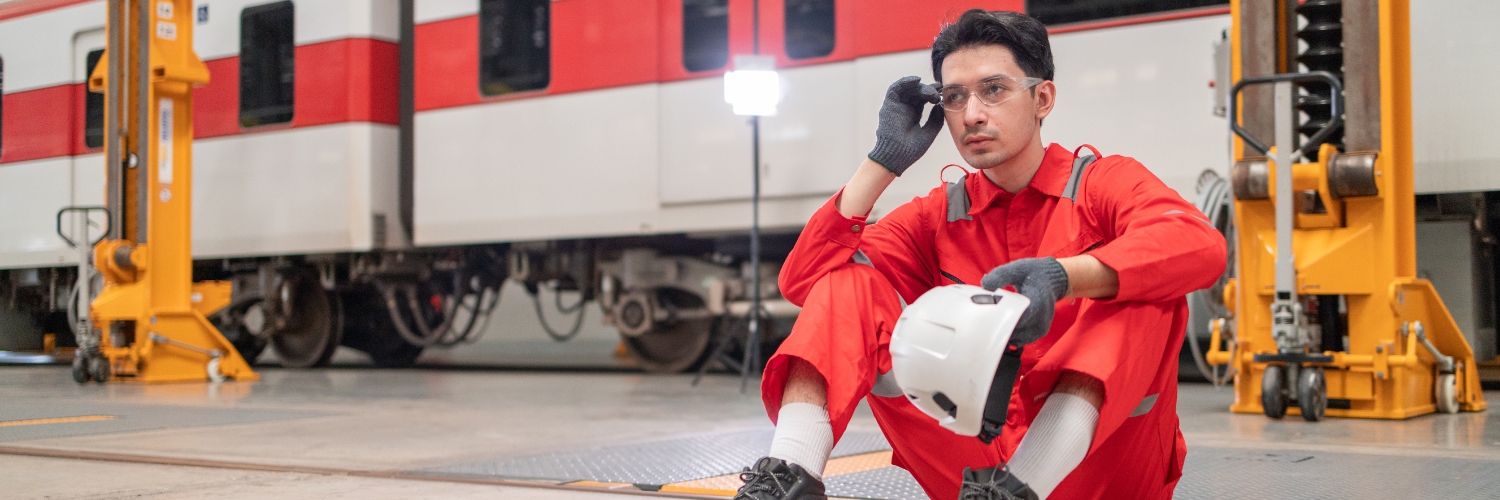
Operaciones ferroviarias más seguras e inteligentes
Cómo las estrategias de mantenimiento proactivo y las mejoras de diseño aumentaron la seguridad y la fiabilidad
- Reducción de los costes de material de mantenimiento en un 29% gracias a la aplicación de RCM.
- Mitigación de los fallos relacionados con la edad en las flotas de pasajeros más antiguas.
- Mejora del rendimiento de primera calidad en un 20% con principios de gestión de activos.
En el sector ferroviario, la seguridad y la fiabilidad no son sólo objetivos, sino que definen el alma de cada operación. Un servicio de trenes de pasajeros, que se enfrentaba a una flota envejecida y a riesgos ocultos, adoptó un enfoque de mantenimiento proactivo para convertir las vulnerabilidades en fortalezas. Aplicando los principios del Mantenimiento Centrado en la Fiabilidad (RCM), el equipo descubrió una serie de problemas que antes pasaban desapercibidos. Se descubrió y corrigió un riesgo de incendio debido a procedimientos inadecuados de limpieza de conductos, y se resolvieron los fallos inducidos por vibraciones en los sistemas eléctricos de puesta a tierra. Se corrigieron fallos en los amortiguadores de aislamiento que permitían la entrada de humo en las zonas de pasajeros, y se subsanaron deficiencias de diseño en las soldaduras de los enfriadores de fuel antes de que pudieran provocar costosos tiempos de inactividad.
Redujimos los costes de material en un 29%, al tiempo que abordábamos riesgos de seguridad críticos, lo que demuestra que el mantenimiento proactivo merece la pena.
Con estas estrategias firmemente implantadas, los resultados hablaron por sí solos. Los rendimientos de primera calidad aumentaron un 20% y una unidad de negocio experimentó un aumento de la producción del 40%, al tiempo que se reducían los costes por tonelada en un 13%. Al aplicar un enfoque holístico de gestión de activos a una rueda de fundición crítica, las paradas no programadas cayeron en picado. Las paradas de producción se redujeron de hasta seis al mes a sólo una o dos, y las de mantenimiento, de hasta seis al mes a una. Al mismo tiempo, los intervalos de mantenimiento planificados se ampliaron de tres a cuatro semanas, lo que permitió un uso más eficiente del tiempo de inactividad y de la mano de obra.
¿Listo para lograr resultados que superen sus expectativas?
Más allá de las preocupaciones inmediatas de seguridad, este cambio de estrategia dio sus frutos en múltiples dimensiones del rendimiento. Se reexaminaron los sistemas de puertas, que solían atascarse a los pocos meses de servicio, y un programa estructurado de ajuste de puertas cada tres meses garantizó un funcionamiento sin problemas y una mayor comodidad de los pasajeros. Con una visión más profunda de cómo envejecían y fallaban los componentes con el paso del tiempo, el equipo diseñó estrategias para gestionar estos problemas antes de que se agravaran, ampliando de forma efectiva la vida útil de la flota sin comprometer las normas de seguridad. Esta previsión también se tradujo en beneficios económicos: gracias a una gestión inteligente de las piezas de repuesto y a mejoras en la fiabilidad, los costes de material de mantenimiento se redujeron un 29%.
Lo más impresionante es que el equipo no sólo se centró en la flota actual, sino que planificó el futuro. Al evaluar un nuevo diseño de bogie de alta velocidad, se aplicaron los principios de RCM para validar y perfeccionar el diseño antes de que saliera de la mesa de dibujo. Como resultado, los fallos potenciales se abordaron de forma proactiva, evitando que se convirtieran en peligros reales y ahorrando a la empresa costosas adaptaciones posteriores. Gracias a la combinación de soluciones inmediatas, mejoras sistemáticas del mantenimiento y validación prospectiva del diseño, esta empresa ferroviaria estableció una nueva referencia de lo que es posible cuando la seguridad, la eficiencia y la fiabilidad guían todas las decisiones.