Minería
Transformación del mantenimiento minero
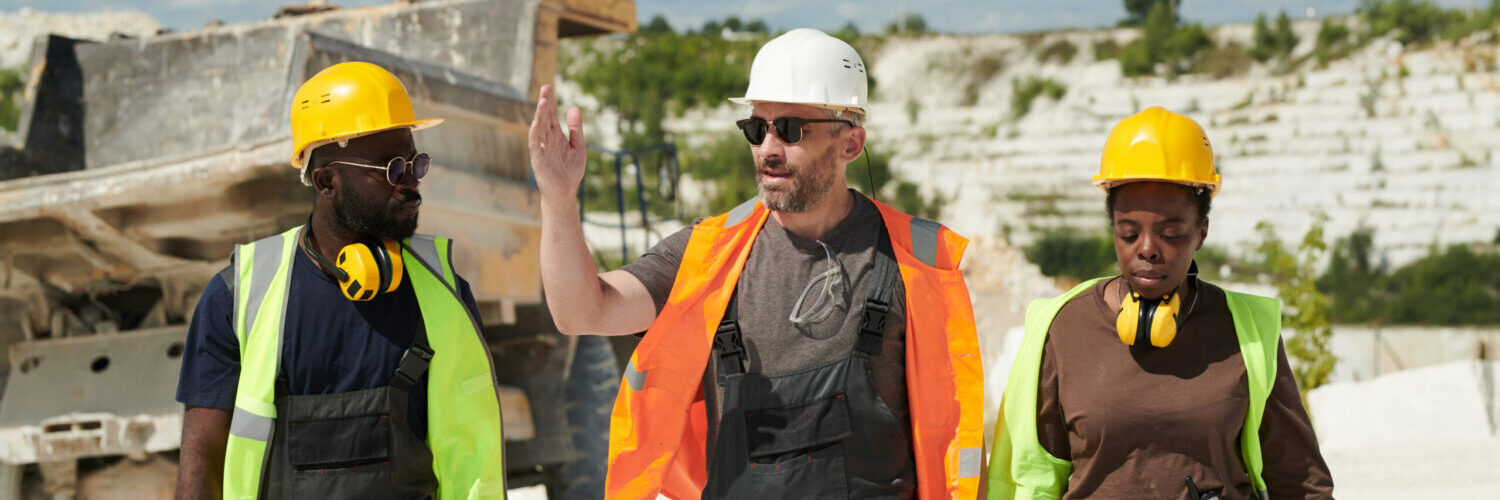
Métricas de transformación de un vistazo
Explore el impacto demostrado del mantenimiento proactivo: desde la reducción de incidentes y costes hasta la ampliación de la vida útil de los equipos y la maximización del rendimiento.
- Reducción en un 75% de los principales incidentes de seguridad del centro.
- Reducción del inventario de piezas de repuesto en 10 millones de dólares.
- Aumentar la vida útil de los camiones de transporte en un 220%.
- De 2 a 3 cortes no programados por semana a 1 en 8 años.
- Entre 2 y 3 años para alcanzar la plena producción y 6 meses para las nuevas instalaciones.
Reducción de los principales incidentes de seguridad de la planta en un 75%.
Reducción de los costes de mantenimiento de la flota móvil en un 8,3%.
El tiempo de mantenimiento de las llaves inglesas ha aumentado un 10%.
Aumento de la producción en un 20%.
En una explotación minera, transformamos su enfoque de mantenimiento y su estrategia general de gestión de activos, con resultados que superaron incluso nuestras más altas expectativas. Mediante la introducción de programas de mantenimiento más eficaces, la optimización de los intervalos de sustitución de los equipos utilizando los principios del Coste del Ciclo de Vida (CCV) y la inculcación de una cultura proactiva, ayudamos a la empresa a lograr resultados operativos y financieros notables.
Desde el principio, la seguridad surgió como una prioridad clave. Nuestras estrategias permitieron a la empresa reducir los principales incidentes de seguridad en un impresionante 75%. Esto no solo protegió a su plantilla, sino que creó un entorno en el que todos podían centrarse en la eficiencia y la mejora continua.
Redujimos un 75% los incidentes graves de seguridad en la planta
Acontinuación abordamos la fiabilidad y los costes de los equipos. En el caso de la flota móvil, redujimos los costes operativos totales en más de un 8% y aumentamos el tiempo de llave inglesa de los técnicos en un 10%. No se trataba simplemente de trabajar más rápido, sino de trabajar de forma más inteligente, anticipando los problemas antes de que se produjeran y garantizando que cada minuto invertido en mantenimiento produjera el máximo valor. De hecho, este cambio hacia prácticas de mantenimiento proactivas generó una ventaja inesperada: el inventario de piezas de repuesto de la planta se redujo en 10 millones de dólares, liberando capital crítico que pudo invertirse en otros lugares.
Los resultados en activos de producción clave fueron especialmente sorprendentes. Mediante una cuidadosa evaluación del ciclo de vida de los equipos y la aplicación de intervenciones estratégicas de mantenimiento, ampliamos la vida útil de sus camiones de transporte de las 50.000 horas previstas a más de 110.000 horas, lo que supone un aumento del 220%. Otros equipos móviles de apoyo, que antes suponían un lastre tanto para el tiempo de actividad como para el presupuesto, se beneficiaron de una estrategia de mantenimiento más sistemática que combinaba una programación eficaz, una ejecución sólida y decisiones informadas sobre la sustitución de activos. El resultado final fue una mayor disponibilidad, un menor coste y un entorno de producción más estable.
¿Listo para lograr resultados que superen sus expectativas?
Uno de los éxitos más espectaculares se produjo en las operaciones de la fábrica. Al centrarnos en mejoras específicas del mantenimiento y dotar al equipo de técnicas proactivas, aumentamos la producción del molino en un 20%, todo ello sin añadir ni un solo empleado más. El molino de bolas de la refinería de níquel es un buen ejemplo: inicialmente se consideraba un activo no crítico, pero en realidad era vital para el proceso. Antes, la refinería sufría entre dos y tres paradas no programadas a la semana. Gracias a un riguroso programa de mantenimiento centrado en la fiabilidad (RCM) y a una adecuada evaluación de la criticidad, las paradas se volvieron prácticamente inexistentes: sólo una parada no programada en ocho años, frente a las 300 que se producían antes.
Quizá la prueba más evidente de la eficacia de nuestro planteamiento se produjo en una mina nueva. Al diseñar un programa integral de gestión de activos y ponerlo en práctica antes de la puesta en marcha, redujimos el periodo de arranque de los dos o tres años previstos a tan solo seis meses. Los objetivos de producción que antes se vislumbraban en un horizonte lejano se alcanzaron -y superaron- mucho antes de lo que nadie había imaginado.
En conjunto, estos logros cuentan una historia de transformación. La seguridad mejoró drásticamente, los costes disminuyeron, la fiabilidad se disparó y la producción aumentó, todo ello gracias a un cambio hacia prácticas de gestión de activos proactivas, basadas en datos y alineadas estratégicamente. Es un testimonio de lo que puede ocurrir cuando una explotación minera adopta una cultura de mantenimiento con visión de futuro y de mejora continua.