Fundamentals of Troubleshooting
Fundamentals of Troubleshooting
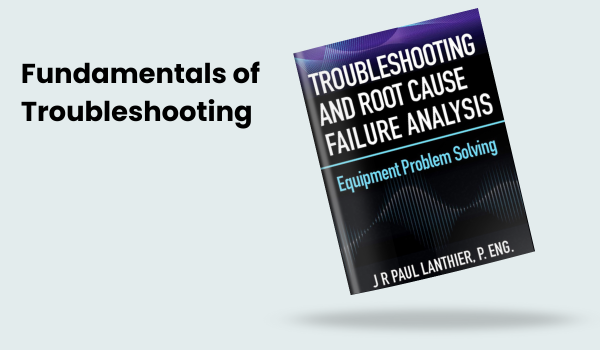
About This Workshop
This comprehensive course combines both rapid troubleshooting techniques and in-depth root cause failure analysis to provide a complete problem-solving toolkit for industrial professionals.
Master two complementary approaches to equipment problem-solving: quick-response troubleshooting for immediate resolution and systematic root cause analysis for permanent solutions. Learn when and how to apply each method while maintaining safety, quality, and efficiency standards.
Key Benefits:
- Reduce equipment downtime
- Lower maintenance costs
- Prevent recurring failures
- Improve asset reliability
- Enhance team problem-solving capabilities
- Better decision-making skills
- Develop systematic analytical approaches
- Improve cross-functional communication
Interactive Learning
The workshop includes practical exercises and case studies to reinforce troubleshooting techniques.
Learning Format:
- Live online or in person
- Interactive discussions
- Real-world case studies
- Hands-on exercises
- Group problem-solving scenarios
- Practical applications
- Structured questioning practice
Who Should Attend
- Technicians
- Operators
Course Content
Introduction to Problem-Solving
-
Basic concepts and definitions
-
Impact on business performance
-
Types of problem-solving approaches